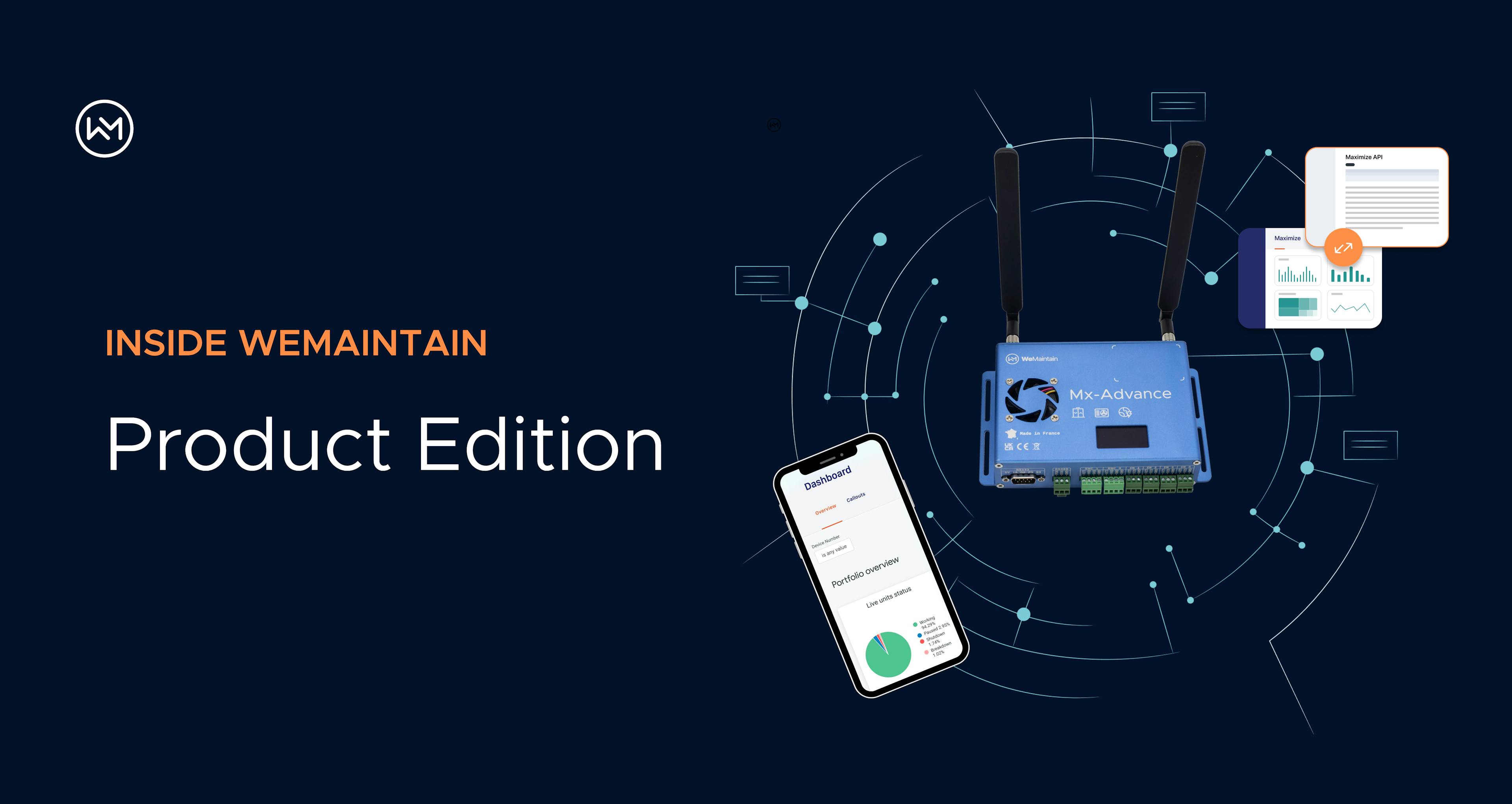
Inside WeMaintain: Product Edition
At WeMaintain, we don’t just do maintenance — we build technology that redefines it. Our DNA is that of a tech company operating in the built environment, not the other way around.
Everything we develop is rooted in one belief: the people on the ground — field engineers, facility teams, ops — deserve better tools, clearer insights, and greater autonomy. By empowering them, we bridge the gap between traditional maintenance and smart infrastructure. Our platform combines IoT, AI, and human expertise to set a new benchmark for performance, customer experience, and sustainable growth.
This Product Edition is our opportunity to share how we build, what we've built, and where we’re headed. It’s a reflection of our vision, our roadmap, and our ambition to lead the building maintenance transformation.
Where It Began
The story of WeMaintain started with a simple observation: for too long, building owners, managers, and field engineers have been limited to minimum standards and outdated processes. Convinced that a more human and efficient model was possible, the co-founders developed WeMaintain to redefine industry standards.
We are transforming maintenance by combining IoT, real-time data, and a digital platform to deliver smarter, more sustainable operations. Our approach empowers field engineers and drives cost savings, performance, and long-term asset sustainability.
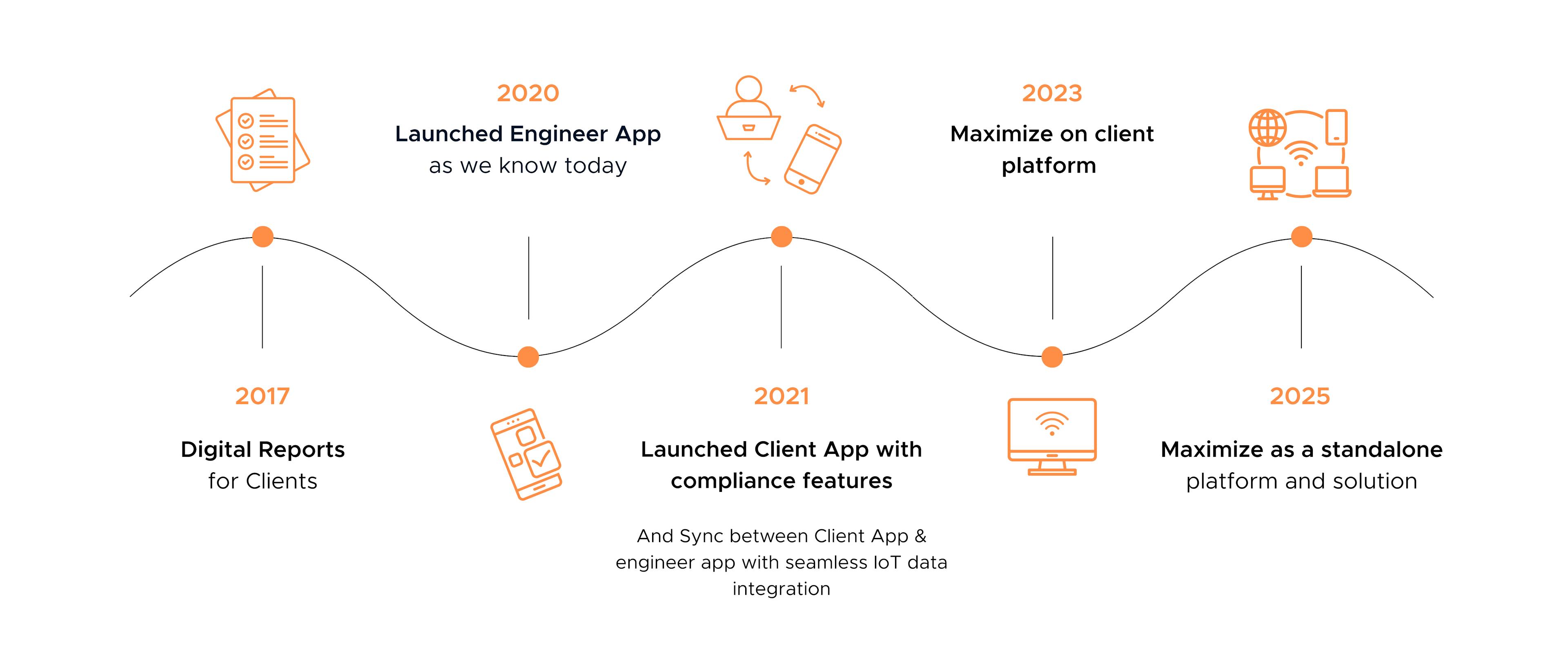
Our Tech Stack
At WeMaintain, our mission is clear:
“To enhance the built environment with a human-led approach, powered by innovative technology, ensuring seamless operations and exceptional experiences.”
WeMaintain’s product is built around two complementary suites: Maintain and Maximize. With our people, on and off the field, being our greatest asset.
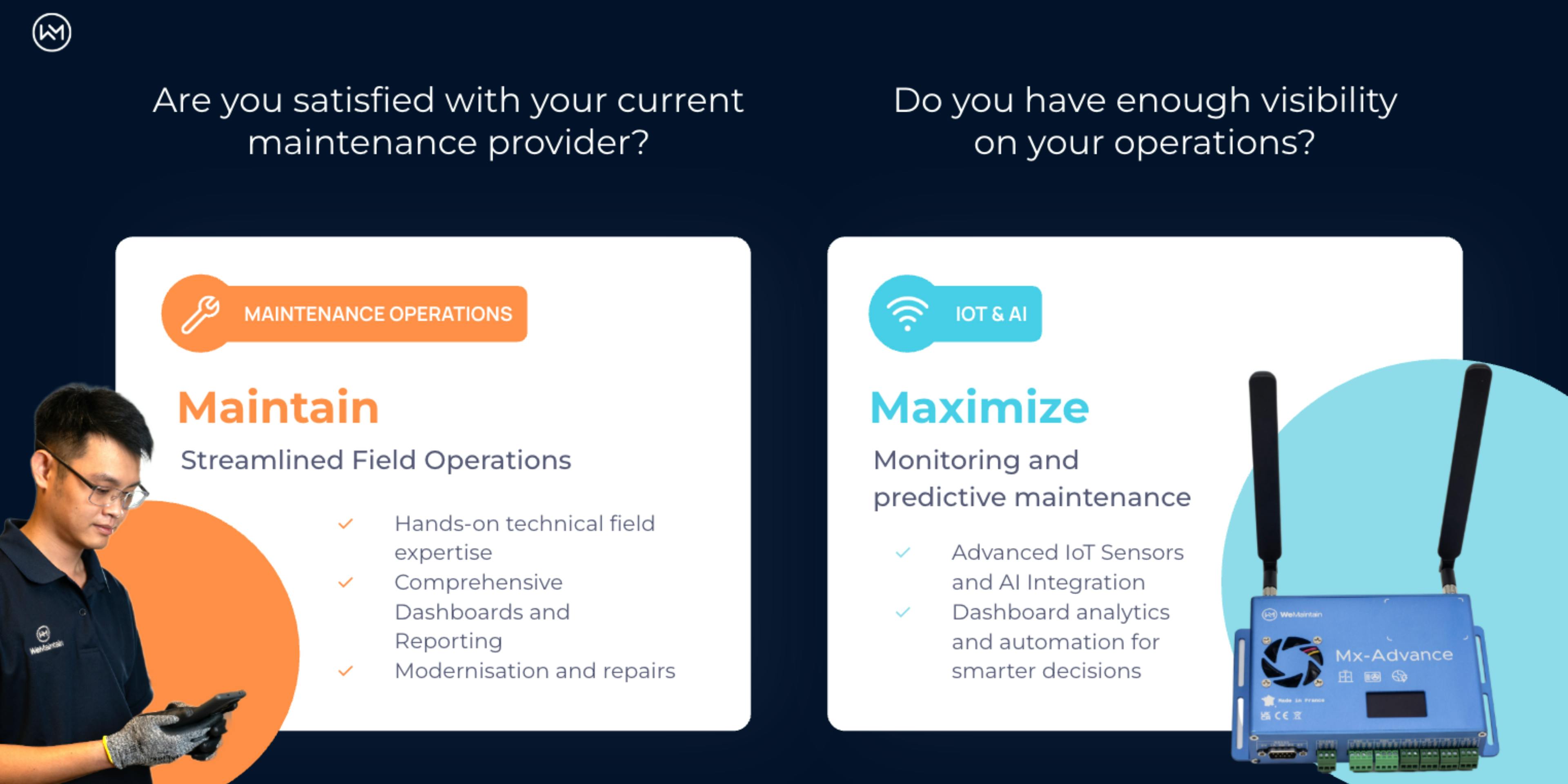
Maintain Suite
Maintenance is still mostly reactive, straining technical teams with limited tools. We believe in empowering our field engineers with the tools, autonomy, and recognition they deserve. Our goal being to combine their experience and expertise to deliver higher-quality maintenance, greater efficiency, and better outcomes on the field. A human-led approach is at the heart of how we build at WeMaintain.
⇒ Smarter maintenance with tech-empowered engineers using our in-house app (Engineer App)
⇒ Real-time insights and system integration for seamless operations
⇒ Full visibility and control of your equipment via the Client App
⇒ Integrated supply chain ensures fast, seamless repairs and fixes
Maximize Suite
To address industry-wide challenges, Maximize takes a holistic approach to performance — from rapid issue response to long-term optimisation and measurable impact.
⇒ Real-time alerts detect breakdowns as they occur — on average, three hours earlier than traditional methods.
⇒ Maximize offers real-time insights that drive smarter, more efficient operations.
⇒ Move from one-size-fits-all to needs-based maintenance plans with insights tailored to actual equipment usage.
⇒Beyond improving availability, we help extend asset lifespan and boost energy efficiency for long-term performance gains.
Our data-driven approach translates into clear actions and measurable ROI.
Our Product Principles
Our approach to product development is shaped by a set of core principles. These guide how we build, prioritise, and evolve our technology.
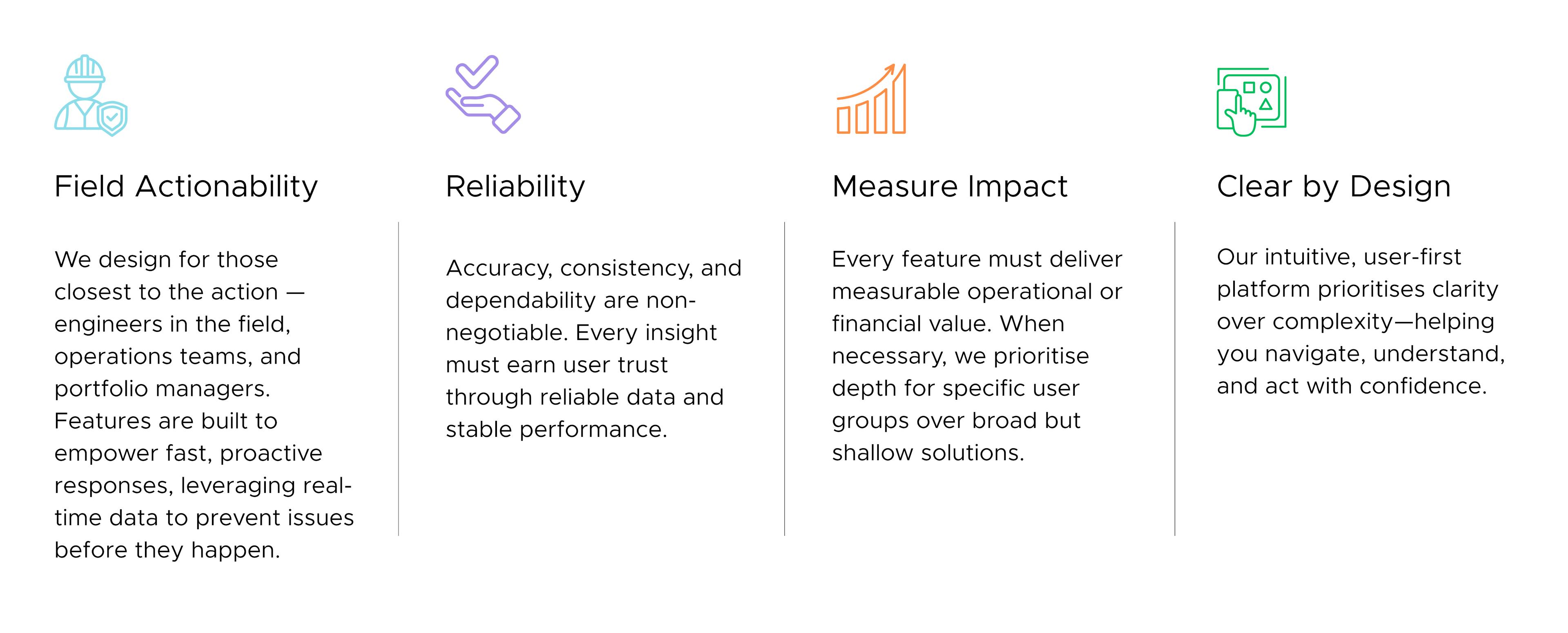
What We’ve Built: A Retrospective
Let’s take a look at what the past 6 months have been like.
During this period, our focus has been on strengthening the foundations of our two suites: Maintain, our service-side platform, and Maximize, our IoT-driven insights platform.
Maintain: Smarter Tools for Service Excellence
We’ve made several enhancements to help engineers and operations teams work more efficiently:
⇒ The new dashboard , along with all the existing features, now provides engineers with a real-time, all-in-one view of their global portfolio
⇒ Engineers can now manage repairs, order parts, and access a global catalogue—all in one app for faster, more consistent service.
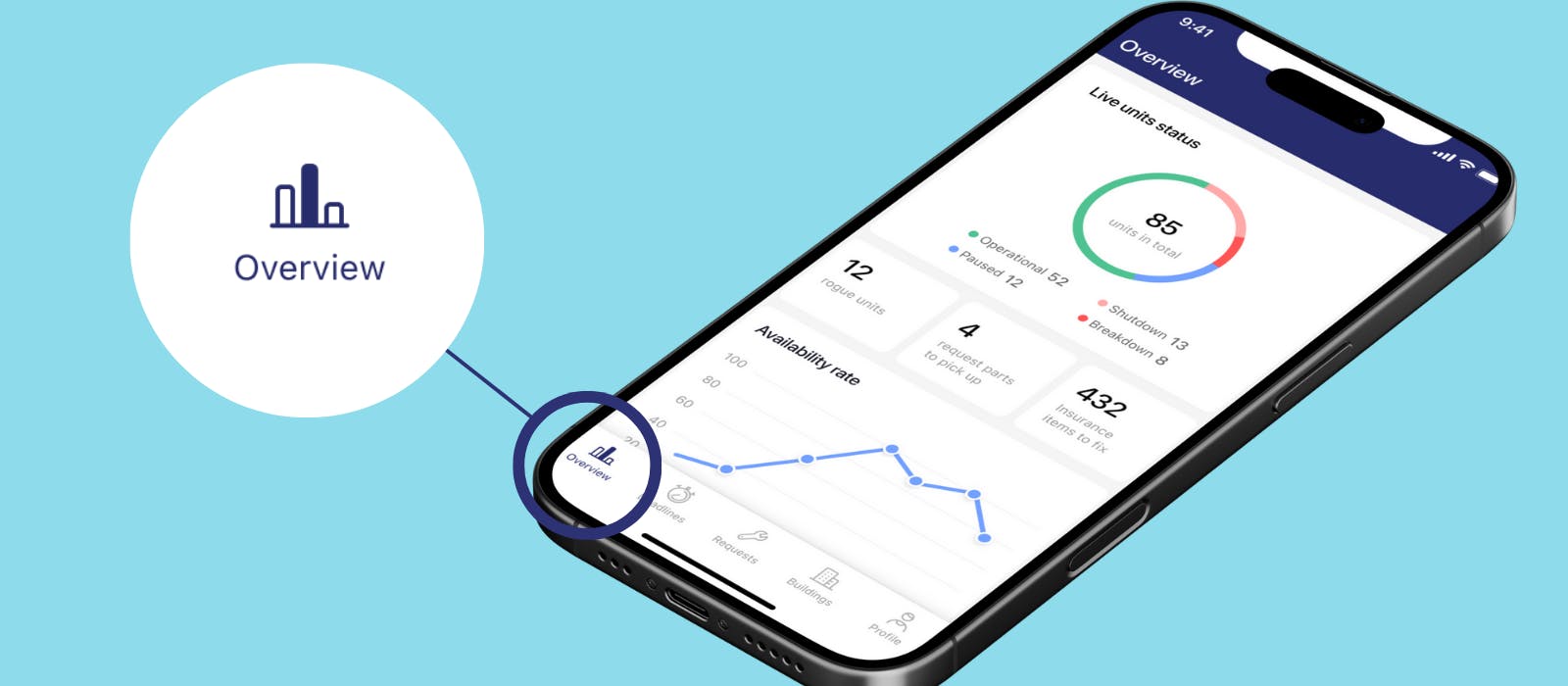
These updates support our goal of providing engineers with better tools, while offering clients increased transparency and control. Our internal product suite is built for the engineers, with the engineers. All features go through a rigorous beta-testing process allowing for refinement and seamless adoption.
Maximize: A Dedicated Platform for Performance Insights
Maximize takes a 360° approach to react to problems, optimise for the long run, and assess performance. One of the most significant milestones this year has been the launch of the new Maximize platform. Currently going through rigorous testing and only open to limited customers at the moment.
The platform was designed to offer a clear, centralised view of how their buildings are performing. It brings together data and insights to help users make decisions faster and act before issues can escalate.
For those deploying Maximize, the platform shows:
⇒ Lift Downtime Alerts – Instant updates when a lift is out of service or back online.
⇒ Improved Downtime Details – A single page with all critical info in one place.
⇒ Escalator Downtime Detection – Now includes downtime detection.
What We Learned Along the Way
The refinement of Maximize was shaped through close collaboration with our clients and our product team. Every feature was refined by real feedback, tested with early adopters, and improved through ongoing dialogue.
“Maximize isn’t just a product—it’s an ecosystem. From IoT sensors to our SaaS platform, we’re solving real-world challenges like uptime and sustainability.
Partners like Groupe ADP push us to go further, and our engineers keep us focused on what truly matters.Co-building with those on the ground makes all the difference.”
— Georgia, Product Manager
A great example of this is our work with Groupe ADP, whose feedback has been instrumental in refining the Maximize experience.
📹 Watch Groupe ADP’s experience with Maximize:
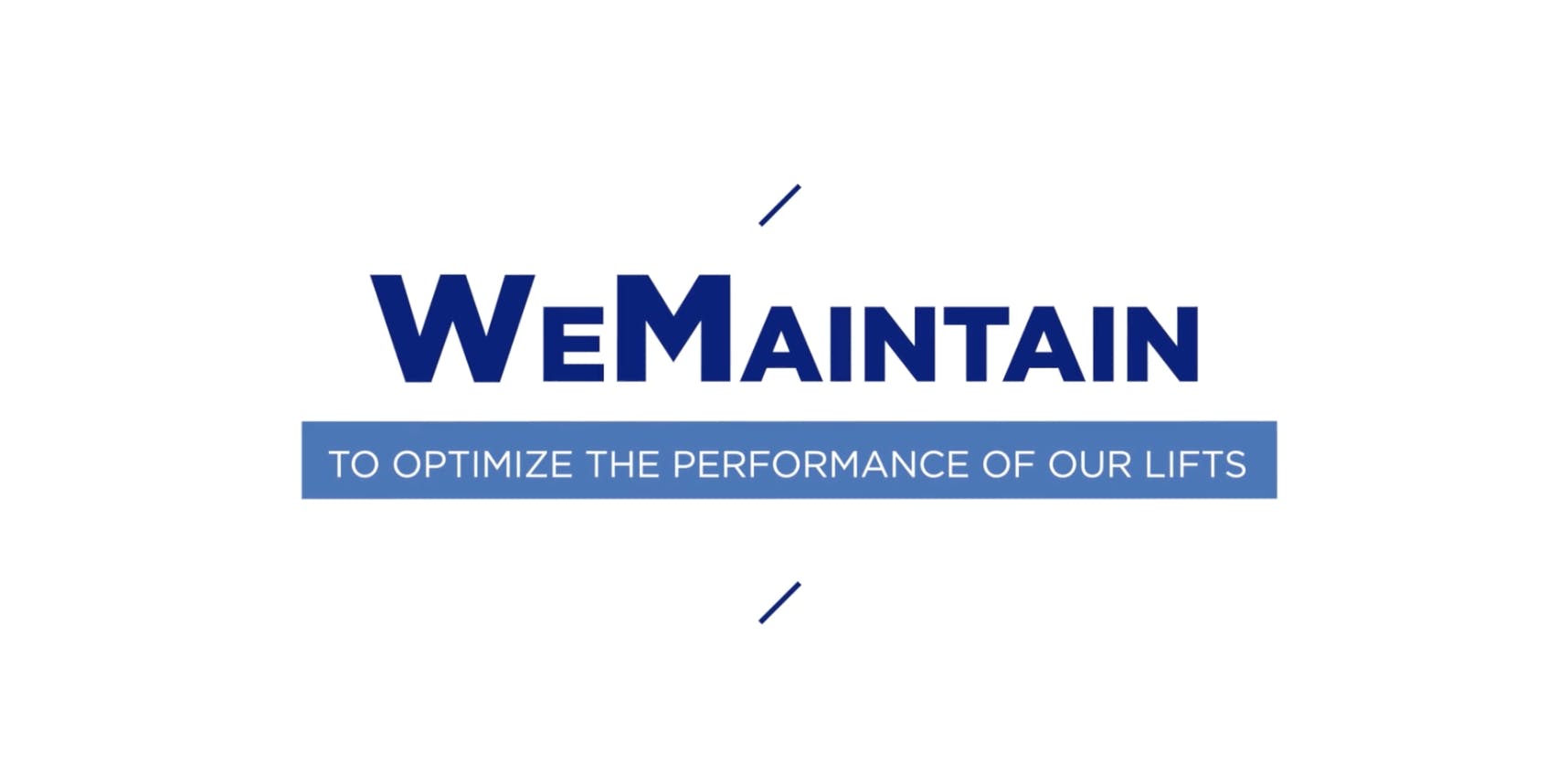
Looking Ahead: What’s in the Pipeline for the Next 6 Months
Over the next six months, we’re focused on building with intent, deepening our existing products while we continue our steady growth.
Maintain: Knowledge, Speed, and Autonomy
Through a combination of in-app training, technical documentation, and a more standardised experience, we aim to support engineers in every situation — from routine maintenance to complex breakdowns.
Key developments include:
⇒ Ai Based training and knowledge platform: A training and knowledge platform, designed to help engineers deepen their technical understanding in real time
⇒ Improved access to manuals and diagnostics: Making brand-specific documentation easily available within the app to speed up fault detection
⇒ Brand-agnostic capabilities: Supporting our engineers with tools that work across all equipment types and manufacturers
These updates help move closer to true brand independence, while reinforcing our human-led model with smart, field-ready tools.
Maximize, expanding to escalators
Alongside the continued refinement of our core features, we’re now extending Maximize’s capabilities to escalators — a significant leap forward in our mission to offer complete asset visibility.
In most of the market today, escalator IoT solutions are limited to simple fault alerts or energy tracking. Maximize goes far beyond this by bringing together real-time field data, contextual insights, and performance metrics in a single, actionable platform.
What makes our approach different:
⇒ Multi-dimensional performance tracking: Beyond energy use, we measure availability, usage patterns
⇒ Insights connected to action: Maximize doesn’t just identify potential problems — it helps teams understand what to do next
⇒ One platform, all assets: Clients managing both lifts and escalators now benefit from unified data, reporting, and decision tools
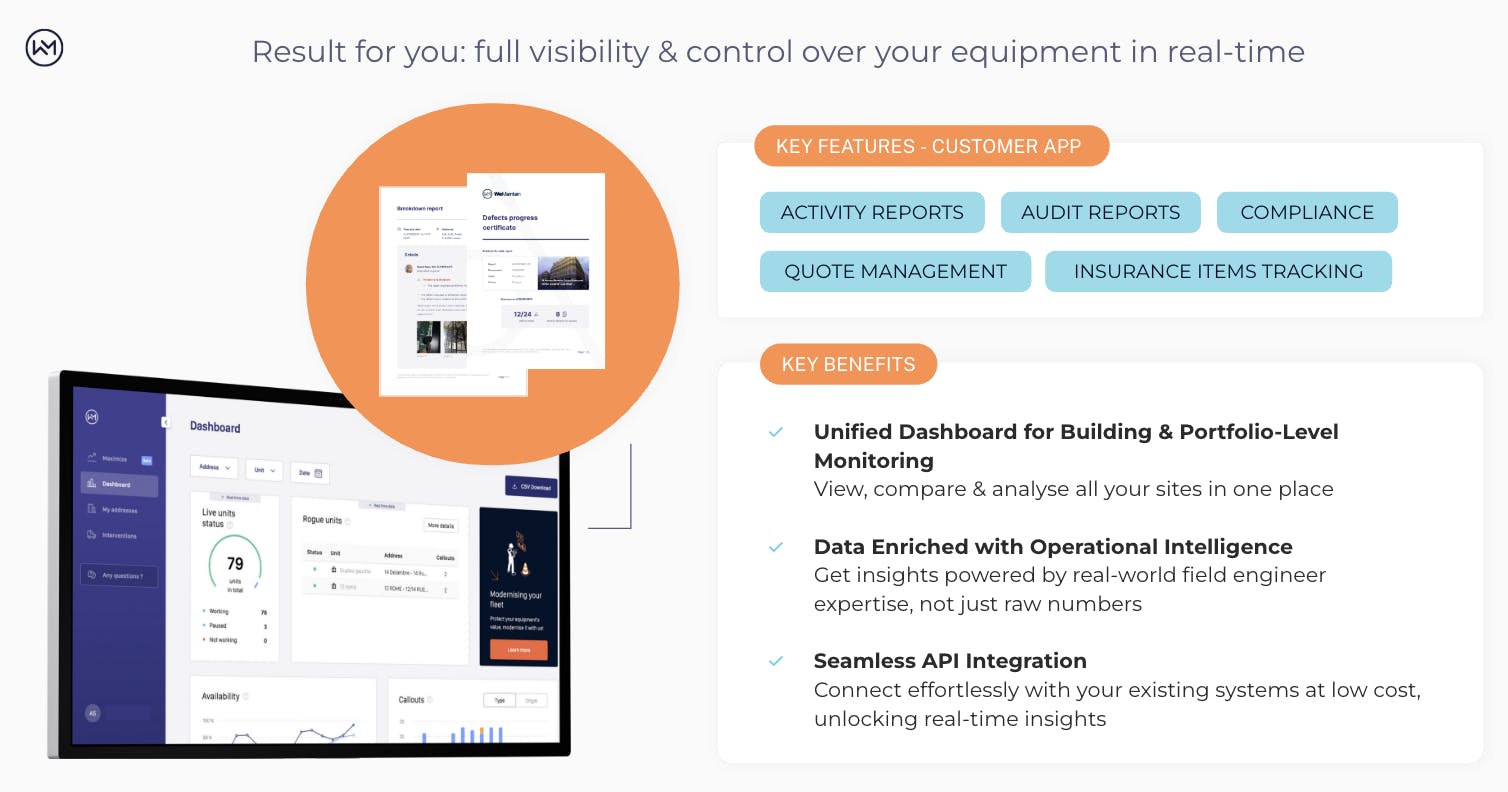
Maximize for Escalators is not a new module, but rather it’s a step toward a more complete understanding of how buildings move and perform. Our unique strength lies in bridging the gap between operations and data, giving clients and field teams the tools they need to make faster, smarter decisions.
Keeping up with the Industry: Picking the right predictive maintenance provider
Predictive maintenance is one of the biggest trends shaping the future of building operations. Everyone in the industry is talking about it, and many are attempting to build solutions around it. But not all approaches are equal.
Most players, particularly OEMs, are taking a controller-based approach, integrating intelligence into their own equipment systems but this comes with critical limitations:
⇒ Vendor lock-in: These systems only work with the proprietary equipment, making them harder to adapt across diverse portfolios.
⇒ Security vulnerabilities: Controller-based systems can be remotely accessed and potentially open to external interference if not managed carefully.
⇒ Invasive deployment: These solutions typically require invasive installation leading to lengthy rollouts.
At WeMaintain, we’ve taken a fundamentally different path. Our non-invasive, brand-agnostic approach utilising IoT sensors gives us, and our clients, key advantages:
⇒ More nimble and scalable: Our sensors work across brands and asset types, making rollout faster and less disruptive.
⇒ Increased accuracy: By capturing real-time field data from multiple touchpoints, we generate deeper insights on equipment condition and usage.
⇒ More secure by design: Our sensors aren’t exposed to the same remote access risks as controller-tied systems, making the data environment easier to protect and maintain.
⇒ Truly independent: We don’t rely on manufacturer-specific data to generate insights. This means more transparency and better benchmarking.
We believe this is the right foundation for predictive maintenance at scale — one that’s reliable, secure, and built for the real operational complexity of buildings today.
Final Thoughts
That wraps up our first Product Update. As the market continues to evolve, it's clear that predictive maintenance will play a defining role in shaping smarter, safer, and more efficient buildings. But to truly deliver on its promise, the underlying technology must be adaptable, secure, and rooted in real operational needs — not manufacturer limitations.
At WeMaintain, we’re proud to offer a solution that meets the moment and looks ahead. Stay tuned for more updates as we continue to build the future of building maintenance — one alert at a time.
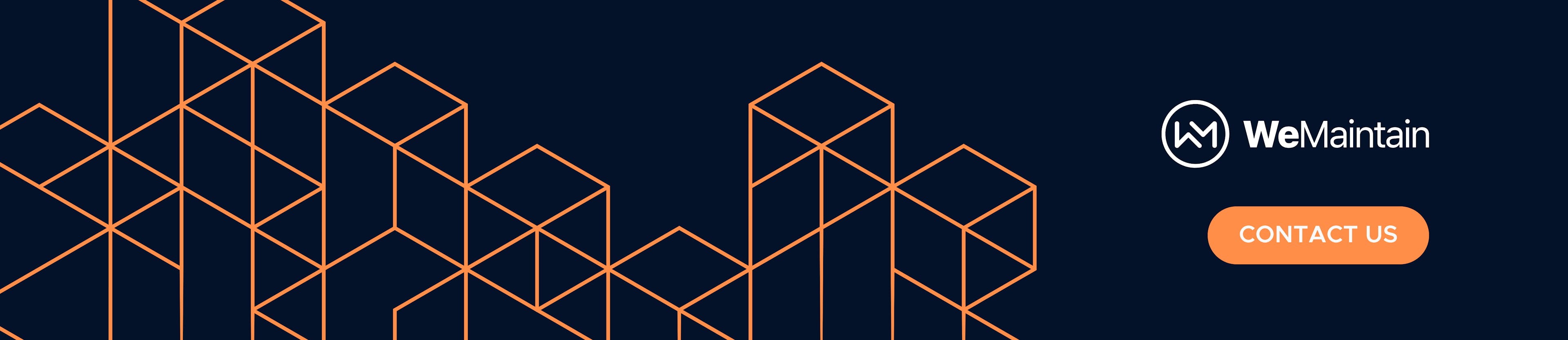