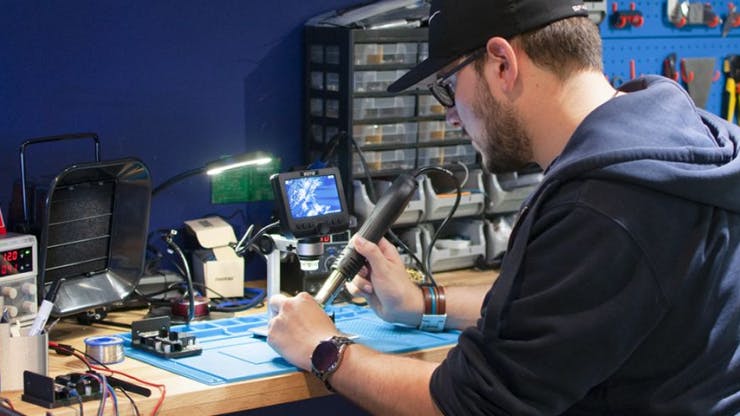
IoT: how our Connected Object Technology enables us to solve complex elevator breakdowns
According to the McKinsey report, in the technical world of elevators, 75% of the value is created by the engineer and only 25% can be automated through technology.
After WeMaintain was created, our first days were spent focusing on redefining the business model around the engineer and the customer, in order to set a new standard for service quality.
At the same time, however, we quickly wanted to develop a data box for our elevators and use the IoT (Internet of Things) techniques to link digital data to the field, improve service quality and reduce breakdowns. After more than 18 months of R&D, we launched our IoT offer to our customers.
The term IoT is used at WeMaintain to refer to our various connected object projects. The most developed of them is the IoT lift box, which is installed on the elevator roof and allows real-time performance monitoring of the associated elevator, second by second.
IoT and connected boxes have been very popular topics in recent years, however it is not always easy to understand the real benefits that this technology can bring in elevator maintenance.
Myself, Olivier Gabriel, Data Science Director, and my two colleagues Damien Weber, IoT Engineer, and Yaya Ba, Elevator Technical Expert at WeMaintain, proposed a more detailed explanation of the possibilities of IoT, using a complex breakdown case we recently encountered with an elevator.
Table of contents:
- Context and IoT box installation
- Actions and problem resolution
- Advantages of the IoT for the maintenance of your elevators
1- Context and IoT box installation
We provide elevator maintenance for a twenty-floor residential tower in the Paris region. A particularity of the building is that it has an "even" elevator (which serves only the even floors) and an "odd" elevator (which serves only the odd floors and the ground floor). These elevators are therefore crucial to the functioning of the building, as in the event of an elevator breakdown, some floors become accessible only via the stairs which can quickly lead to long delays and potentially dissuade residents from making trips at all.
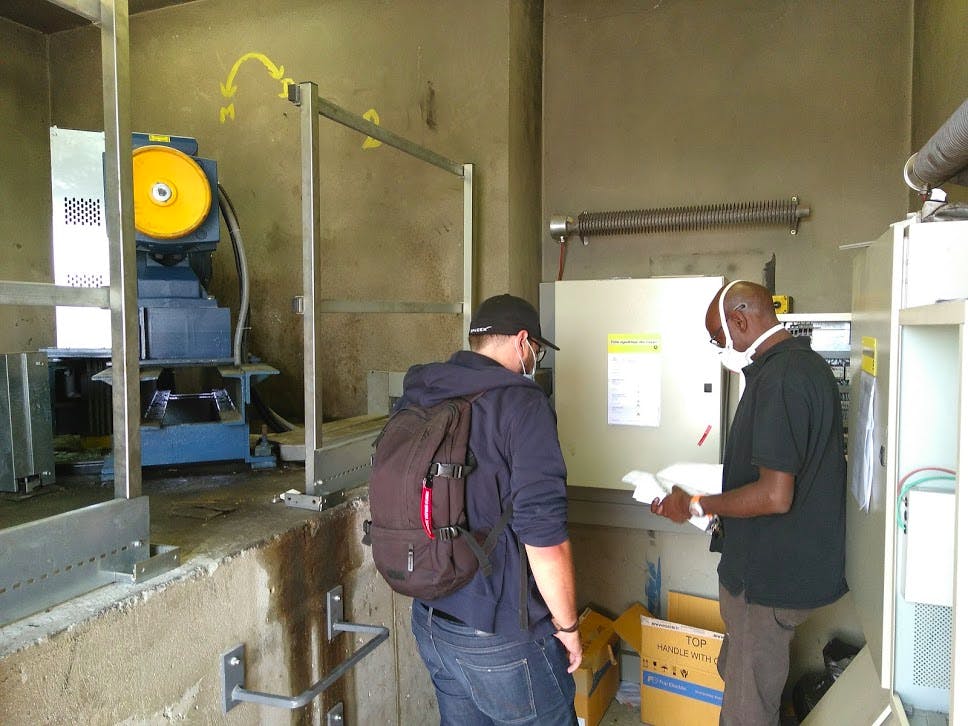
For several weeks, the odd elevator had been experiencing repeated breakdowns that were difficult to interpret. On certain occasions, we were notified of a breakdown on the elevator only to find that once we arrived on site, it was functioning normally.
Intermittent failure: recurring failure of an elevator for a limited period of time, making it difficult to diagnose the failure.
Since our fault finding analysis is mainly based on observations made in the field and the breakdown reports issued automatically, we knew that we could go further by utilising our technology to complete our analysis.
Installation of the IoT box
In consultation with the technical experts in the field, we therefore decided to install an IoT box on the odd elevator on May 12, 2020 to be able to monitor the elevator constantly, thanks to the data received in real time.
Printed in 3D in our Parisian facility, the IoT box is simple, quick to install and compatible with any type of elevator, it does not require any specific adjustment of parameters upstream.
Within one hour, the box was installed on the problematic elevator and we were able to start recording the data transmitted by the IoT in real time and analyse it remotely.
Evaluation of IoT data
The data recorded by the IoT is sent to our servers and stored in a database. Our tools then allowed us to monitor this data remotely, producing graphs that retrace the position of the elevator with an indication of time. The IoT data then allowed us to detect abnormal behaviour in the elevator that could indicate a possible failure.
Thanks to the IoT data, we were able to trace the position of the elevator car in real-time and record the successive openings of the doors.
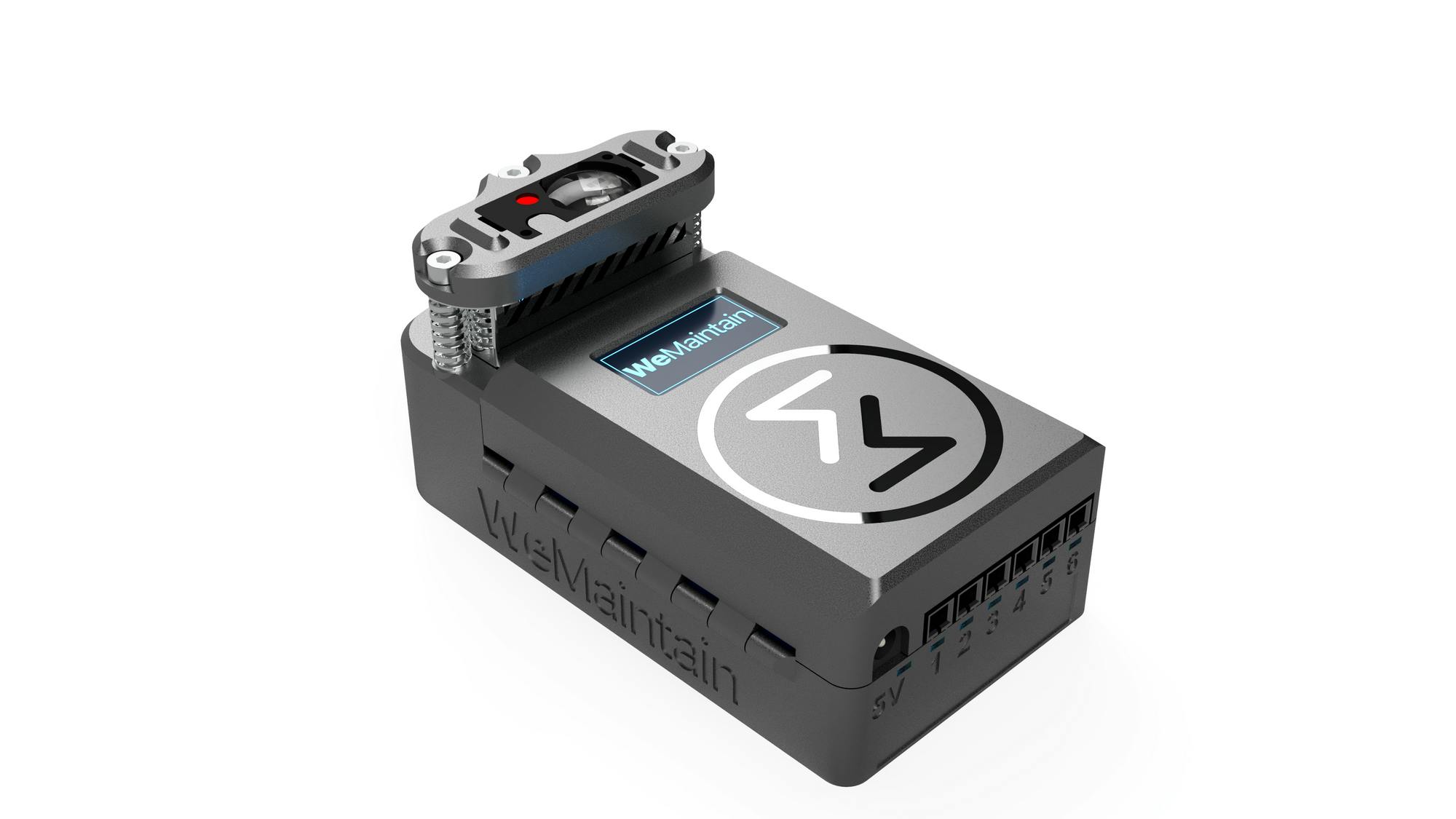
On the above graph, the blue dots indicate the position of the elevator as a function of time. The different floors are represented by the purple horizontal lines. On the graph above, we can thus read the first (leftmost) movements:
- the elevator left from the 4th floor at 9:50 am,
- it went down to the ground floor,
- before leaving for the 7th floor,
- ...
The parts of the graph coloured in red mean that the doors are closed, those in green mean that they are open and those in yellow mean that they are moving.
2. Actions and problems solving
A few days after the IoT was installed, the three of us went to the site to compare the data recorded by the IoT with the observations in the field.
This allowed us to identify several specific problems with the operation of the odd elevator and to understand them as a whole.
Thanks to the statistics gathered by the IoT, we were then able to draw up a concrete action plan to solve these problems, which we then presented at a meeting before the customer.
In a very short period of time, we were able to make a diagnosis on the elevator and to mobilise all of WeMaintain's expertise to provide solutions to the problem.
Olivier Gabriel, Data Science Director at WeMaintain
The identified problems
The comparison of the IoT's and the field's data confirmed our hypotheses and allowed us to identify three main problems:
- Door opening/closing cycles:
The data gave us insight into the door opening/closing "cycles". The elevator would try to close its doors, it wouldn't succeed, so it would bring them back to the open position, then it would make another attempt... We could observe a sequence of one hour (!) during which this cycle continued. From the data transmitted by the IoT, we noticed a design problem with the doors, whereby the landing doors were too heavy for the associated door equipment.
- Braking management:
The readings taken on the elevator showed that there were problems with braking management. In real terms, the elevator sometimes stopped in the direction of descent, between the second floor and the first floor.
- Loss of position:
On some particularly recalcitrant elevators, the controller (elevator control computer) sometimes "loses" the position of the car. In these instances, the controller orders the elevator to go up to its uppermost stop to "find" and confirm the position of the car. The IoT allowed us to confirm that such "position losses" were happening on this elevator.
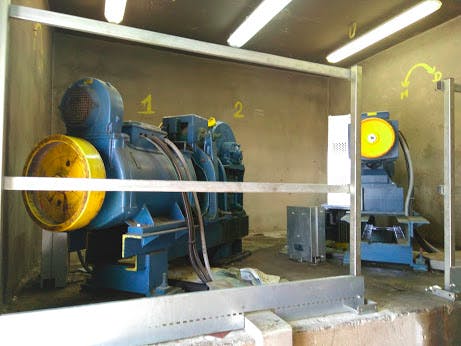
The proposed solutions
Based on the previous observations, we were able to make diagnoses based on the expertise of Yaya Ba, Technical Expert in elevators, and thus propose a series of solutions to the customer:
- Opening/closing of doors - unsuitable carrier motors:
Following our observations, we concluded that the landing doors were too heavy for the carrier motors. Replacing these elements with more suitable parts will improve the long-term reliability of the elevator and solve the problem of the repeated door open/close attempts.
After identifying the cycles where the doors could not close, we changed the carrier motor, which was undersized in relation to the size of the landing doors.
- Braking management - system reconfiguration:
From the IoT data, we concluded that the configuration of the odd elevator is similar to that of the even elevator. The origin of the braking problem lies in the controller itself. A thorough reconfiguration of the controller will therefore be necessary.
- Loss of position - link between controller and elevator car:
Elevator position losses are related to weaknesses in the trailing flex, a kind of "umbilical cord" of the elevator, present in the entire elevator shaft. To solve the problem of position loss of the elevator, we proposed to change the trailing flex which was not sufficiently reinforced. By using a reinforced cable, the elevator no longer loses its position and the associated failures disappear.
Elevator controller: computer that manages the essential commands of the elevator (its position, acceleration speed, etc.).
Trailing flex: Electric cable that connects the cabin and the control cabinet
Door actuator: Motor and mechanism on the car that allows the opening and closing of the elevator doors.
3. Advantages of the IoT for the maintenance of your elevators
The IoT box has several important advantages for our daily maintenance work.
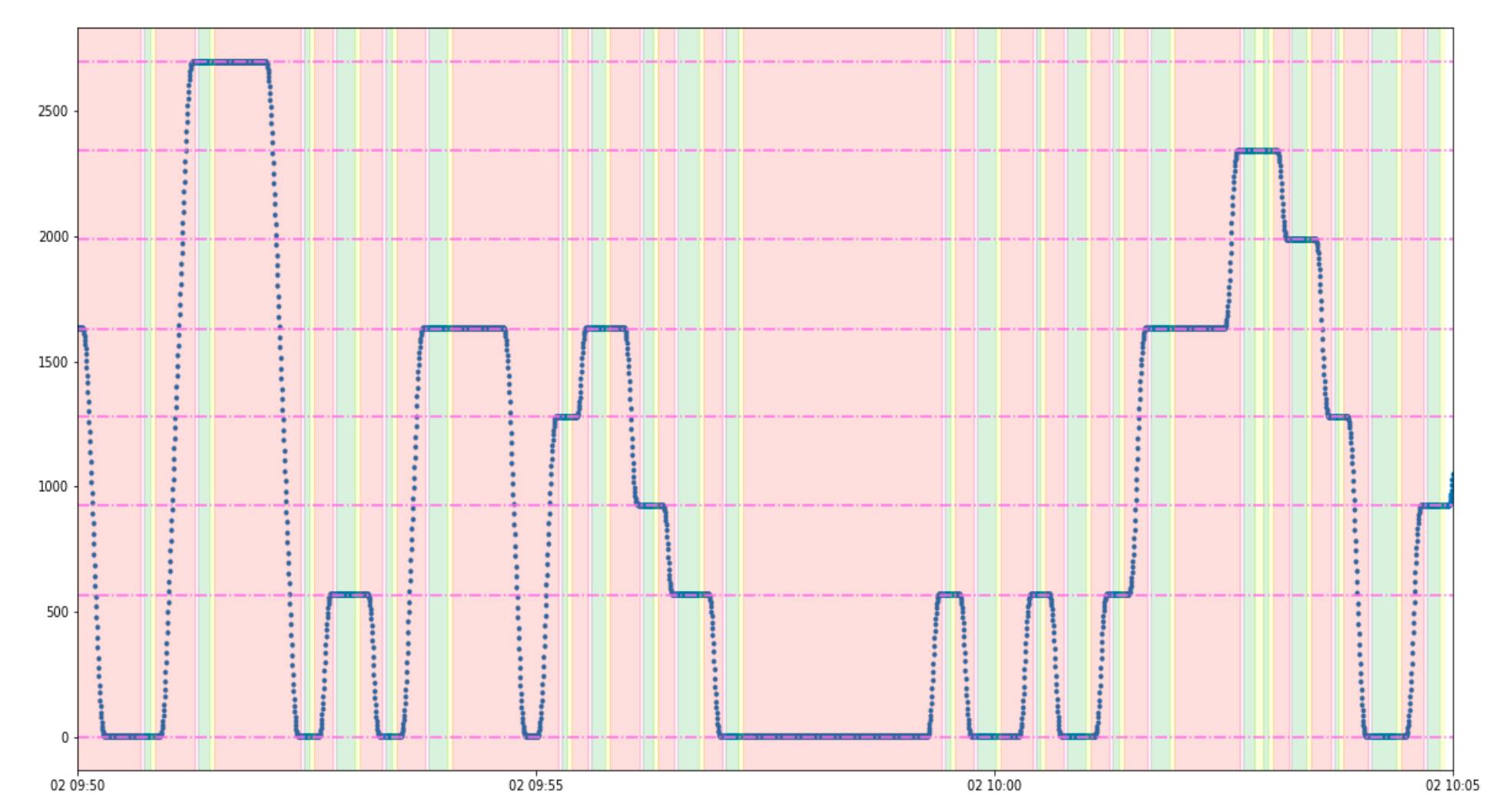
Improve remote elevator monitoring
The IoT box initially allows us to improve the monitoring of our elevator fleet remotely.
Placed on the elevator, the box retrieves information and sends it by 4G to the Cloud. Composed of a telemeter that measures the distance between the roof of the elevator car and the ceiling of the shaft, it provides us, among other things, with the following information :
- the position of the elevator in the shaft
- an indicator of fully open or fully closed (elevator) doors
- an indicator of speed of travel
Thanks to the data transmitted, we can follow in real time the operation of the devices second by second: their position, their path between floors, their speed of acceleration or the opening of doors on each floor.
Our customers also have access to an interactive dashboard that presents the data through quarterly reports, via an application that allows them to visualise the interpreted data. This allows them to choose the period of time they wish to view.
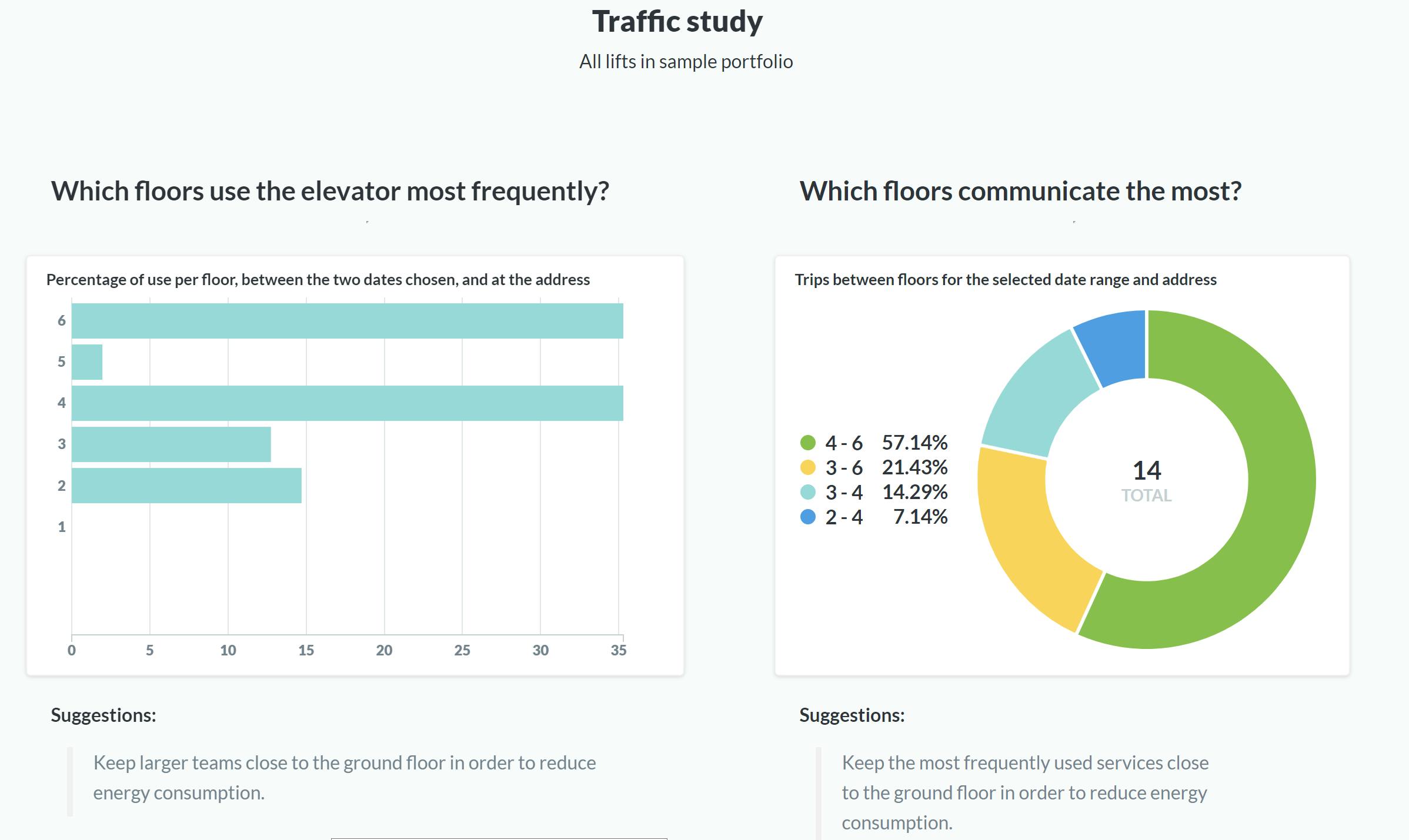
The box allows us to precisely quantify the traffic on a given elevator and thus analyse it remotely.
One of our customers noticed that the door on the fourth floor of his building was opening and closing erratically. The IoT data allowed us to see that the doors were closing, but not completely. The IoT allowed us to provide the customer with a more complete diagnosis and to correct the settings very quickly.
Damien Weber, IoT engineer.
Troubleshooting
The IoT data enables us to improve our overall method of remote fault diagnosis, to better anticipate complex problems and to anticipate the solutions to be adopted.
By comparing historical data with current ones, we can better detect any elevator malfunctions that may indicate a potential failure downstream. It also gives us the possibility to better direct the fault finding of breakdowns once on site.
Better preparation of the intervention of the engineers on site
By remotely diagnosing the failure using IoT data, engineers and technical experts are aware of the characteristics and problems in progress on each elevator, allowing them to better prepare their intervention beforehand.
The information provided by the box allows the dedicated engineer to go on site before the breakdown is identified by users, but also to devote his time to the actual intervention, instead of having to make a lengthy diagnosis with no added value for the customer. In this context, the box usefully complements WeMaintain's technical expertise.
Benoit Dupont, co-founder and CEO.
This represents a considerable time saving for the maintenance work of engineers in the field.
In the case of intermittent breakdowns, for example, the box constantly monitors the elevator which makes it possible to confirm and quantify malfunctions as they occur. In the longer term, our goal for the IoT is to move in the direction of predictive maintenance, i.e. to predict and qualify failures in advance.
Provide better customer service by bringing together data and human expertise in the field.
The great complexity in the elevator world is that, with some work, we can gain access to a lot of data from very different sources (field, IoT, etc ...), but they are compartmentalised and not reviewed together, which prevents a 360 analysis of the situations. At WeMaintain we have worked from the beginning to set up a structure that allows the different data to communicate instantaneously.
By bringing together data and human technical expertise in the field, our model allows us to optimise elevator availability, reduce downtime, and provide our customers with a better understanding of their assets to improve their day-to-day experience. The information is transformed into useful indicators for the customer. After analysing elevator car movement (traffic analysis, most frequently used floors, counting people in the car, etc.), the owner and manager have a better understanding of the routes taken by occupants. At the customer's request, WeMaintain can then optimise these routes, in particular to reduce waiting times related to certain elevators.
This collaboration is a good example of how WeMaintain is mobilising all its skills, in the technical and digital fields, to improve the service offered to our customers.
Olivier Gabriel, Data Science Director
If you want to find out more, head to our website www.wemaintain.com