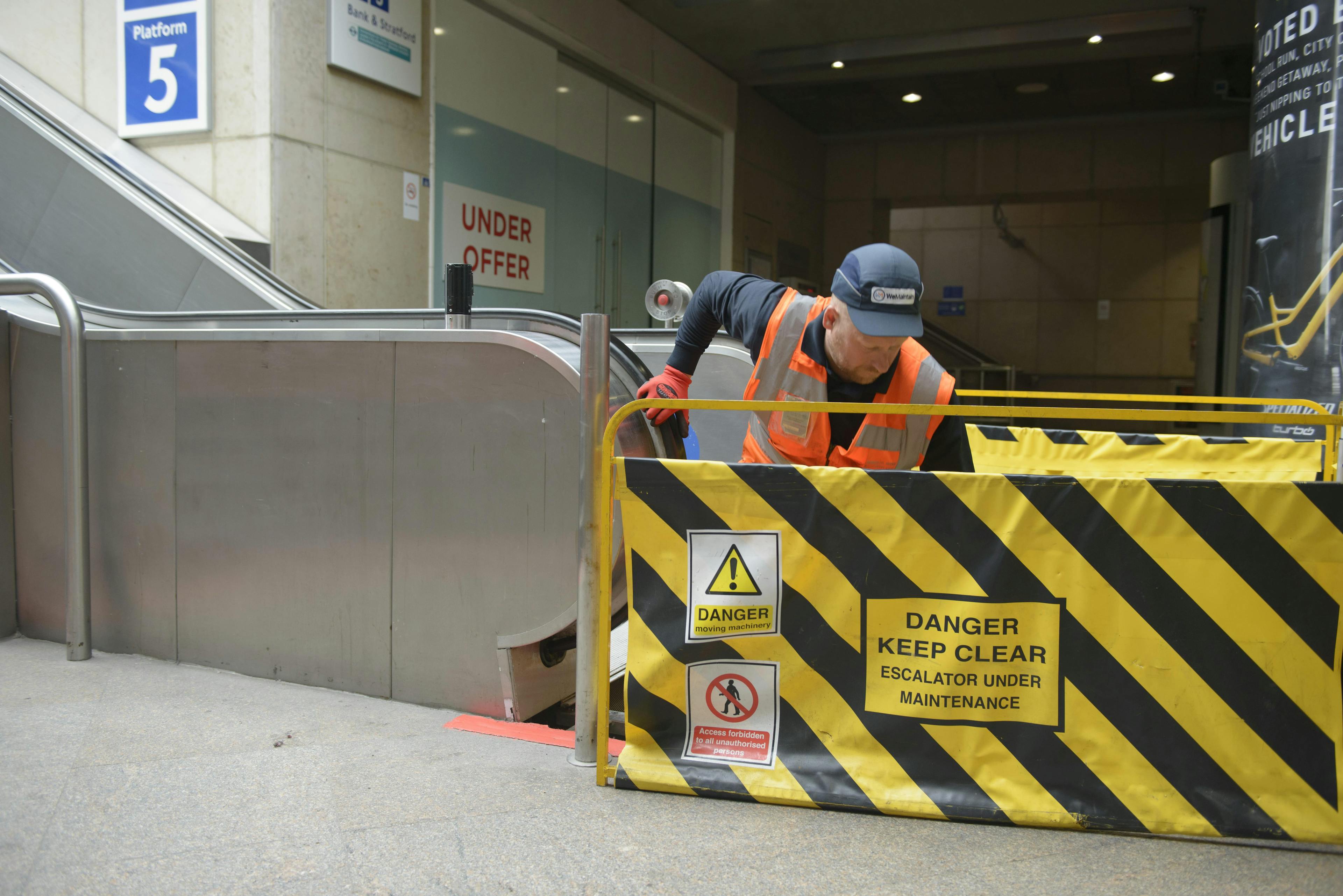
Critical equipment
Why has my escalator stopped?
Why has my escalator stopped?
We’ve all had to grudgingly walk up a motionless escalator that’s stopped working, which always seems to happen on a day when you have a heavy bag to carry.
But what has caused the escalator to stop?
In this short article, we’ve outlined a few of the main causes for a faulty escalator, and more importantly, how this can be prevented in the future.
Causes
- Original design: It could be that from the very beginning, the type of escalator design and structure were not appropriate for its location. For example, equipment that was designed for indoor usage being installed outdoors can result in issues down the line.
- External influences: These could be things such as items getting caught in the tracks or high temperature affecting the electrical components that operate the escalator.
- Age of equipment: Like most things, age can affect the reliability of equipment. It could be that it’s been a few too many years since installation and the equipment needs an upgrade.
- Equipment malfunction: Escalators are designed with safety as a paramount concern which means there are a number of safety features that, if activated, can stop the lift. Usually a malfunction relates to these safety features have been activated unnecessarily.
- Worn components: Worn components pose a risk to the functioning of an escalator and if left unchanged, can cause breakdowns.
Prevention
Luckily, your escalator can have a long and problem-free life when properly taken care of and with proper maintenance. Here are some of the preventative measures that you can take to ensure this:
- Quality, regular maintenance: Having an experienced engineer regularly check over the equipment means adjustments can be made and worn components identified proactively, therefore heading problems off at the pass. A maintenance contract containing regular maintenance visits is imperative.
- Worn components replaced before failure: Regular maintenance allows us to catch potential issues before they develop into something more urgent and costly, such as anticipating when a part or component needs replacing before it fails.
- Original Equipment Manufacturer (OEM) supply chain for parts: WeMaintain’s app WeSupply, is a global digital supply chain created to acquire and deliver parts with the fastest lead-time. Having these components readily available means less downtime for our customers.
- IoT monitoring: In addition to regular maintenance visits, WeMaintain offers a data solution using our IoT technology. Installing an IoT device on an escalator means you can monitor it remotely, giving you greater visibility of your equipment’s operation and help to identify and resolve issues ahead of time.
- Modernisation & upgrade solutions: To ensure your equipment continues to function regularly, it’s necessary to carry out condition assessments and plan for any modernisations or upgrades, in order to maximise the lifecycle of your escalators.
Find out more
Unfortunately, escalator breakdowns are a common and daily occurrence in the vertical transportation industry and can disrupt the flow of people in a building.
Escalators have an average lifecycle of 20 years, based on environment, usage and maintenance schedule. WeMaintain can offer different contract options, modernisation and upgrade solutions to extend this lifecycle for a number of years, avoiding the need for a full replacement and disruption to your building. And in the short-term, WeMaintain can maximise the availability of your escalators, using a combination of technology, highly skilled engineers and quality maintenance.
Our average escalator call-out rate (number of breakdowns / number of escalators maintained) of 0.68, within our goal of 1.75, is a testament to WeMaintain’s successful business model.
Contact
Contact WeMaintain for better, smarter maintenance of your escalator: cheryl@wemaintain.com