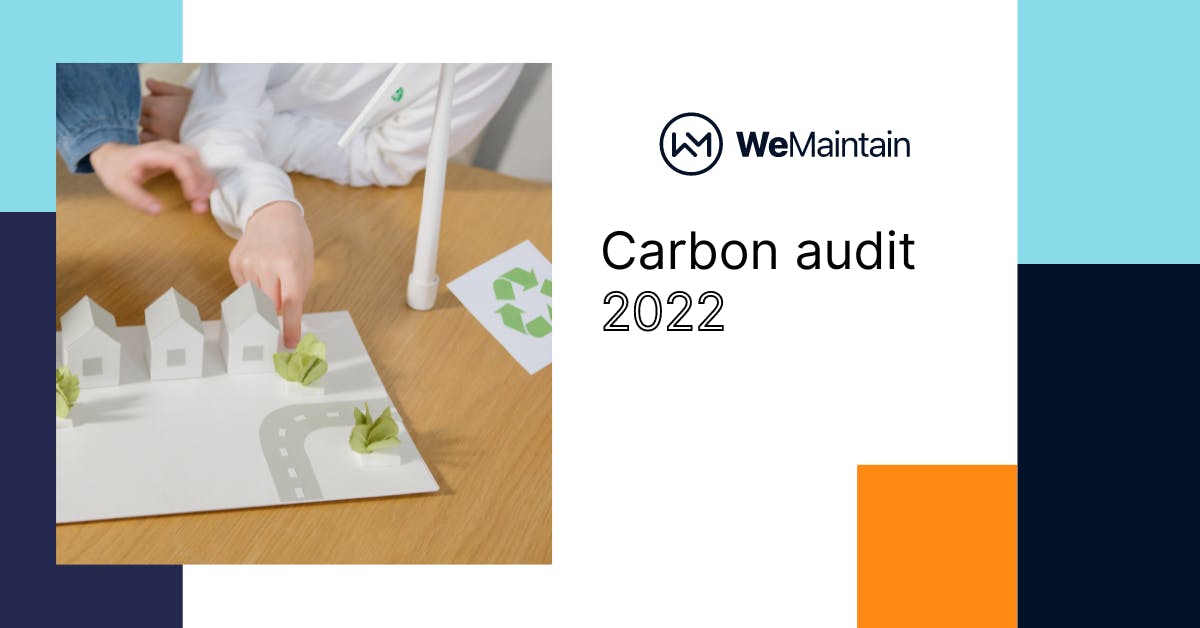
On the road to Net Zero: lessons learned from our first carbon assessment.
Context
You have probably already heard about the carbon footprint and how it has become the preferred tool for companies to assess their impact on the environment. Our employees have a strong ecological awareness and they regularly ask questions about the environmental strategy of the company. We, therefore, decided that the carbon audit would be the first step of our carbon reduction roadmap and identifying the greenhouse gas (GHG) emissions of our company would help us understand just where we stand. Going forward, we would then set numerical reduction targets and finally, agree on a meaningful action plan. This project was definitely more challenging than we could have thought. At the start, we were thinking that the first results would be available within 3 months but this was way too ambitious... In the end, all the obstacles were lessons learned and we believe it is just part of the process. Before we go into more detail and share our experience with you, let's first define what a carbon footprint is.
Definition
People, products and organisations all have a carbon footprint. Your amount of GHG emissions is made up of a variety of sources including the food you eat or the t-shirts you wear. Measuring the amount of greenhouse gases emitted with your direct and indirect activities is a good way to better understand the main source of the problem. Each type of emission can be assigned a scope 1, 2 or 3:
Scope 1 covers emissions from a source directly owned by the company; it can be, for example, from fuel consumed in our fleet of vehicles.
Scope 2 are indirect emissions coming from the energy purchased and used by the company; for instance, the electricity consumption of our offices.
Scope 3 encompasses the indirect emissions (upstream and downstream) from sources not controlled by the company; in this case we refer to business travel, procurement or waste.
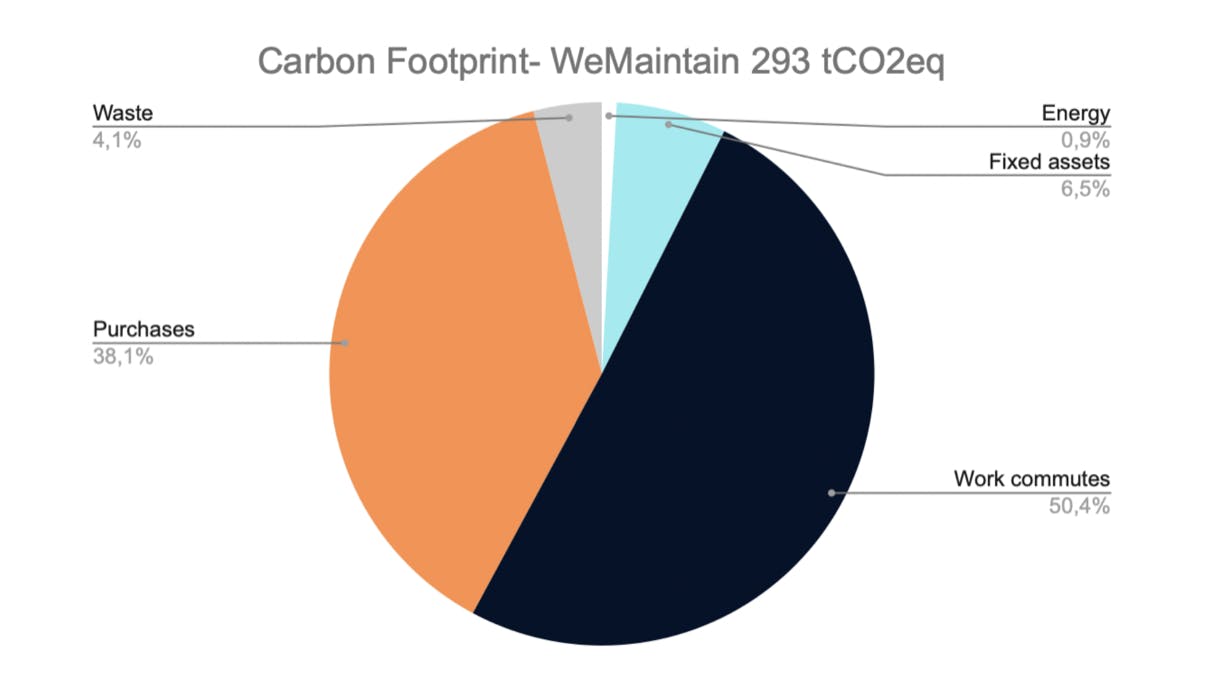
Process
WeMaintain partnered with Kapstan, a French environmental consultancy, to evaluate the company’s carbon footprint for the year 2021 in France. The assessment covers scopes 1, 2 and 3 but does not include operations in the UK and Singapore. We made this choice intentionally as we knew that the first carbon footprint would be tedious and we were not necessarily prepared for it. So we decided to concentrate our efforts on one country to become familiar with the data collection process. We started small with the aim of expanding our analysis to the whole company in the forthcoming assessments.
The data collection took us several months as we found that sometimes, the information was in different places or the exact figures couldn’t be found. Financial data is quite easy to gather but physical information is definitely more challenging. When measuring the impact of our purchases, for instance, we quickly understood that we would have to adopt a more in-depth and precise approach. We had to sort the orders placed in 2021 by category (electronics, lighting, plastic etc.) and determine the weight of each spare part. It was not an easy task considering we had to analyse a list of 2000 ordered spare parts. Moreover, we had minimal information: name of the spare part, price and the quantity purchased. This obstacle prompted us to find a way of automating the process a bit more and so now the spare parts are automatically classified on the platform we use.
Results
As a result, we could identify 5 emitting areas:
- Work commutes 🚗
- Purchases 🧾
- Waste ♻️
- Energy ⚡
- Fixed assets 🏢
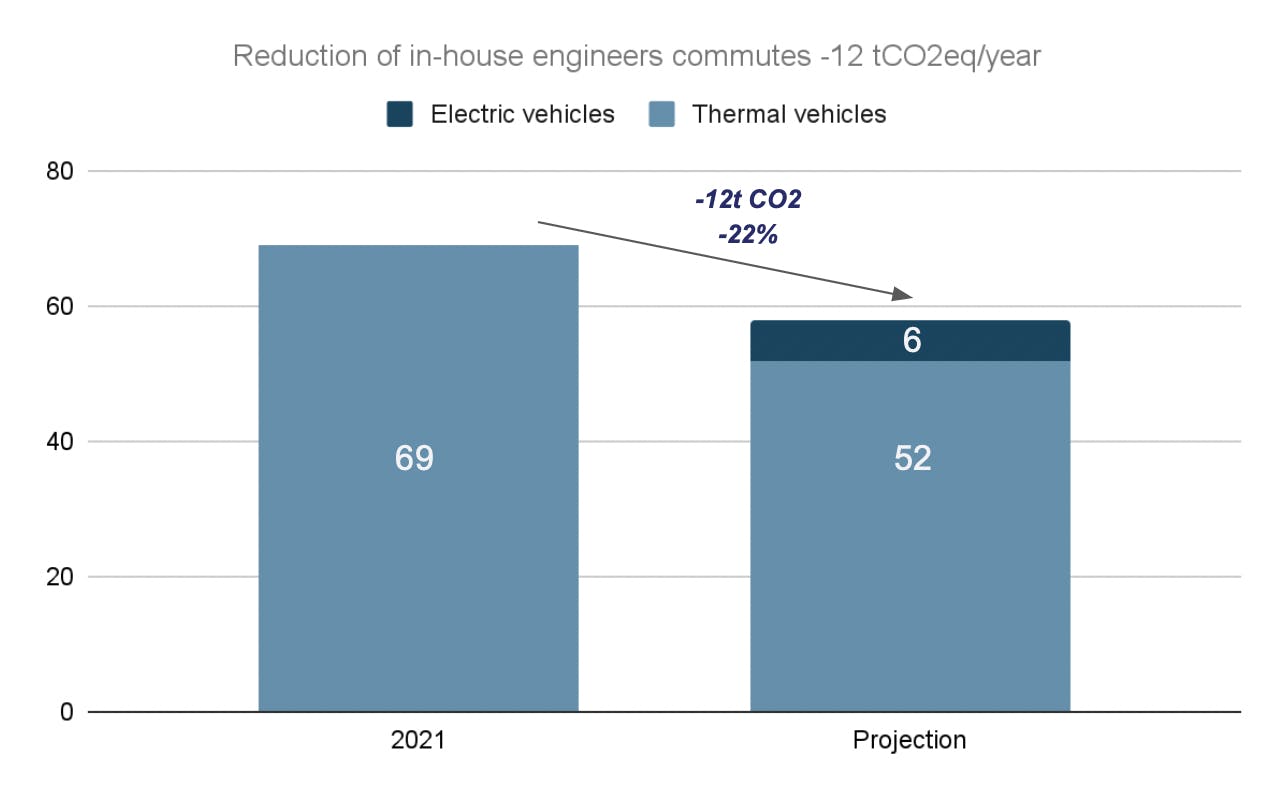
We initially thought that these results would help us establish quantified reduction targets. But when drawing up our action plan, we realised that the reliability of the data collected could be improved because some of scope 3 emissions are difficult to quantify precisely. This carbon footprint undoubtedly gave us an overview of the most important areas of emissions but saying that WeMaintain emitted exactly 293 tCO2eq in 2021 is a bold statement. Accuracy is acquired over time: this is something this project taught us.
Although they did not allow us to define a reduction target, we used these results to prioritise the projects to be addressed. With the help of Kapstan, we defined and established meaningful solutions.
Carbon offsetting
As a first step, we decided to “cancel out” the impact of our emissions through the Climate Neutral Now initiative launched by the United Nations by investing in two projects.
The first project concerns a 10 MW biomass power plant located in Chimur, India. The aim of the project is to efficiently use available biomass fuels such as rice husk (bran) and crop residues in the region for electricity generation. The electricity generated will be sold to the state electricity grid for sustainable economic growth, environmental conservation through the use of biofuels and the reduction of GHG emissions. The project will also help meet the growing demand for electricity.
The second is a wind power project in South Korea. It should help the government to minimise dependence on fossil fuel imports and create domestic power resources, which will have added economic benefits.
Both these projects helped WeMaintain become what we call a carbon neutral company. Carbon neutrality means getting to a state in which an organisation's GHG emissions balance out to zero. Spending money in compensation might help but it does not erase the footprint we create. To achieve Net Zero, we must go even further and reduce emissions in line with the latest climate science. We have therefore committed to estimate our GHG emissions, try to reduce them and communicate our results every year by signing a commitment with the United Nations.
Subsequent projects
Work commutes, purchases and waste having been identified as the biggest source of emissions for the company, we decided that our first initiatives would tackle these three areas.
WeMaintain firstly invested in electric vehicles in September 2022. We equipped five of our engineers with an electric Renault Kangoo.
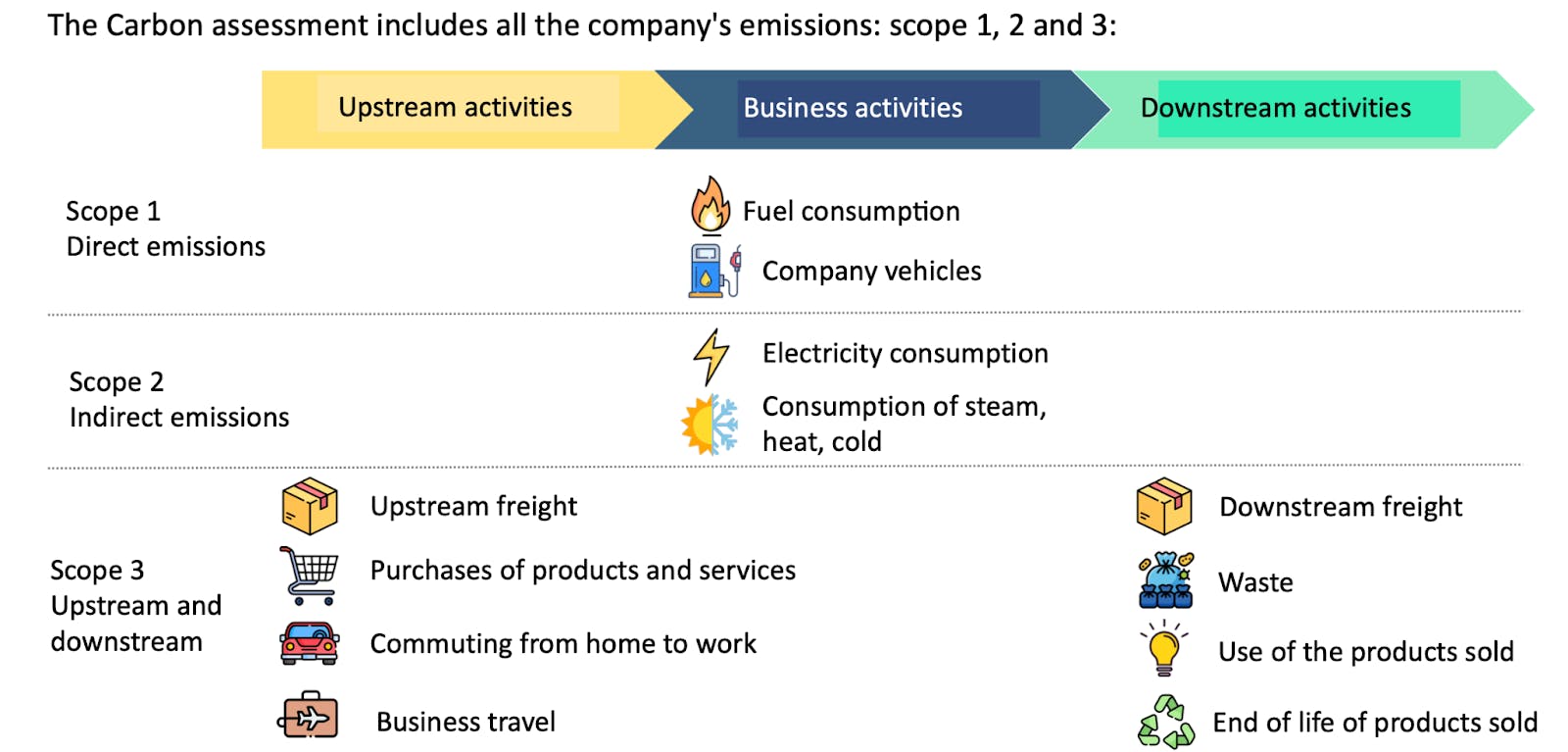
We were concerned about the fact that electric vehicles emit more carbon than petrol vehicles at the time of their manufacture. But according to the ADEME, the French agency for ecological transition, an electric vehicle emits less CO2 today even when compared on a full life-cycle basis. The table below shows that the impact of an electric car is actually 2.35 times lower than that of a petrol car in France.
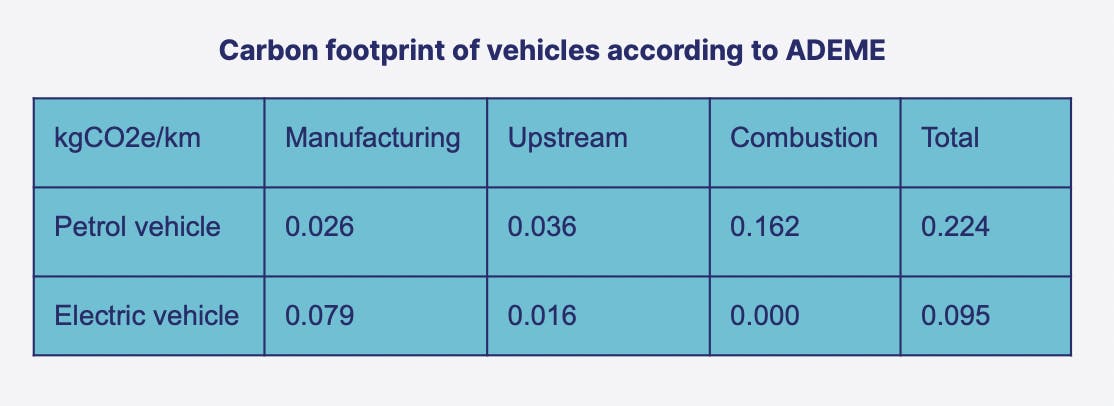
Our carbon consultant estimated the reduction potential of this project at 12tCO2, assuming that our fleet size remains the same next year. As this investment seems to show its effectiveness, we would like to have a 100% electric fleet in the long run.
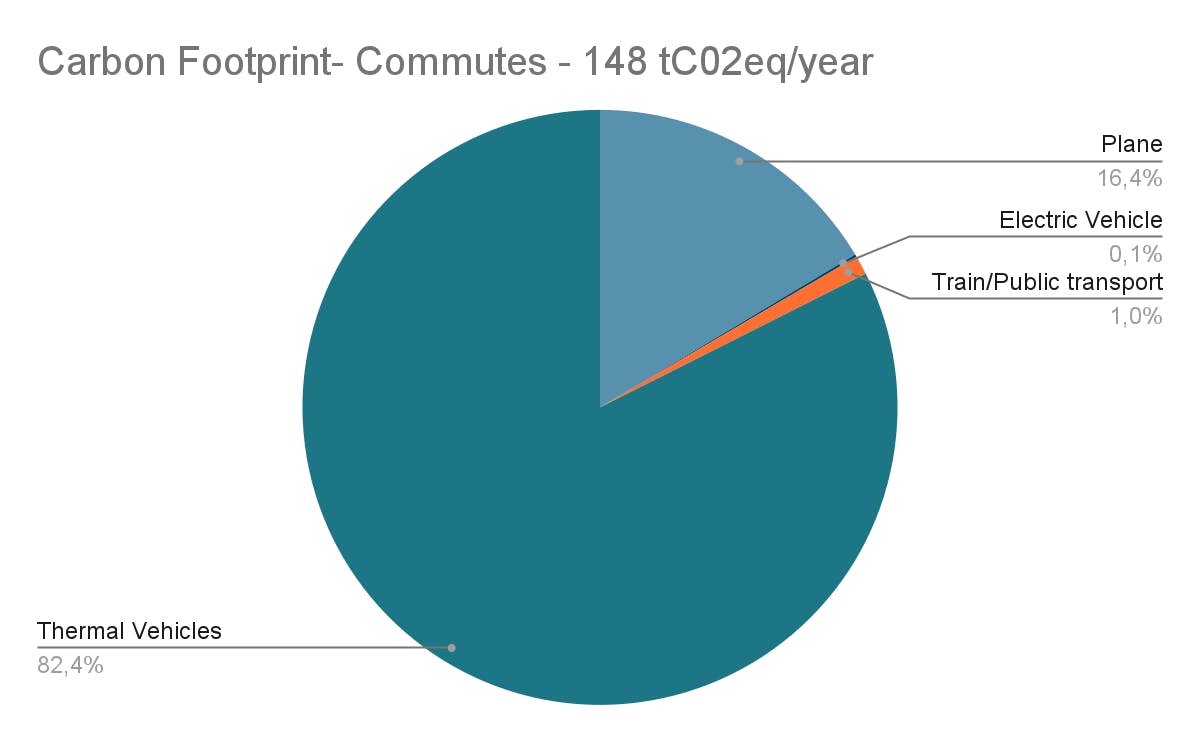
Secondly, we decided to address a major project for our procurement policy. What’s complex about this source of emissions is that they come from the use of third parties and intermediaries and we cannot simply cut ties with them. Because we are not a constructor, we buy spare parts every year and have to respect safety regulations. Escalators, lifts, and fire & safety systems must comply with certain standards and we cannot maintain these using spare parts from just any brand when carrying out maintenance. Because our suppliers are essential for us to continue to maintain equipment, we need to engage with them. The multitude of suppliers we work with makes it difficult to enforce a new policy but, we are determined to endorse higher standards of social, ethical and environmental practices. We, therefore, started with an analysis of our biggest suppliers to see whether they show interest in CSR practices or not. Ideally, we want to place orders with our certified suppliers in priority and track this number monthly. Our carbon footprint also taught us that we should request further analysis of certain spare parts that are particularly polluting. Electronic and metal parts, for instance, should be subject to a product life cycle analysis by our suppliers.
Lastly, we had to think about how we could track our waste more efficiently. We don't really have a place where waste is centralised. The engineers sometimes dispose of the waste at the customers' premises and sometimes they go to a waste disposal centre. Thus, we cannot accurately assess how much waste is produced each year as a result of maintenance work. We discussed it with DeliverMe, our spare part delivery subcontractor, and decided to stock our waste in their warehouse. At the end of the month, we would call on Les Ripeurs to evacuate the waste and provide us with a follow-up on the quantity of waste collected.
Conclusion
Our first carbon footprint took a long time and is probably not perfect in terms of accuracy. We had to solve several problems and review our approach whenever we faced an obstacle, but at least it gave us a clearer idea of where we’re standing right now and taught us many valuable lessons along the way. Most importantly, this assessment helped us identify the most emissive activities and establish a roadmap that prioritises the projects falling into these areas. We must now think about how we can automate the data collection and equip ourselves with the right tools to facilitate the process. As stated earlier, we started small with one country but all the steps we have gone through make us feel more ready for a global carbon footprint. The step-by-step culture really is something we value at WeMaintain. We don’t want to make too many promises if we can’t honour half of them. We believe that it makes more sense to concentrate efforts on a few small projects in order to make progress towards bigger initiatives. Our approach is to start small but think big.